Dual Magnetron Sputtering (DMS): The Basics
Veröffentlicht Juni 11, 2014 von Dave Christie
Magnetron sputtering systems are used to deposit complex layer systems on solid substrates and flexible webs for various uses, including display, flexible electronics, packaging, lighting, decorative, architectural, and automotive applications. Some of the layers are compounds, which may be dielectrics or transparent conductive oxides (TCOs). These layers may be deposited by reactive sputtering. Dual magnetron sputtering (DMS) has been widely used for reactive deposition in inline and roll-to-roll coaters. In DMS, the magnetrons alternate roles as cathode and anode, depending on the polarity of the power supply output. DMS eliminates the need for explicit, separate anodes. This is one of its main advantages, since explicit anodes require regular maintenance and are a source of unwanted particle generation. In dielectric deposition processes, explicit anodes can stop working when they become covered with insulating material, the so-called disappearing anode effect. Magnetrons can be planar or rotatable. Now, it is common to use a pair of rotatable magnetrons for reactive DMS; an example of an industrial-scale dual rotatable magnetron system is shown in the picture below. These processes and approaches seem straightforward. It is the subtle variables that make them challenging for industrial applications, where the process must run continually day after day. Uneven target consumption can be a significant issue for DMS systems. The cause can be imbalances in power and reactive sputtering working point between the two magnetrons.
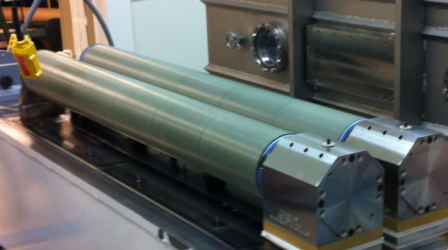
Industrial-scale dual magnetron system for large-area glass coating
In the reactive DMS process, material is sputtered from the surface of the target and travels to the surface of the substrate. The reactive gas combines with the target material at the surface of the substrate to form the compound. The difficulty comes from another surface reaction. The reactive gas also reacts with the surface of the target (it is, in fact, sub-planted into the target surface), forming a compound at and slightly below the surface. When a small fraction of the target is covered with compound, it is said to be in the metallic mode.
When a large fraction of the target is covered with compound, it is said to be in the poisoned mode or fully reactive mode. The compound typically has a lower sputtering yield than the target material, so deposition rate is reduced. In some cases, the sputtering yield for the compound is only 10% of the sputtering yield for the pure target material. There is an intermediate operating point, called the transition mode. It is between the metallic and poisoned modes. In the transition mode, it is possible to deposit films with high optical quality at high deposition rates. A feedback control system is required to maintain operation in the transition mode, with voltage, reactive gas partial pressure, or optical emission used for feedback [1]. Consequently, many reactive sputtering processes are operated in the fully reactive mode, where lower rate is accepted in return for film quality and simpler control.
References
[1] W.D. Sproul, D.J. Christie, D.C. Carter, Thin Solid Films, Vol. 491 Issue 1-2 (2005) 1.