Aircraft Weld & Bond Inspection
投稿 1月 07, 2023 によって Advanced Energy Editor
Preventing Aircraft Communications and Navigation Disruptions: Testing the Ground Path to Minimize Lightning or Static Discharge Impacts
Lightning poses the most challenging and dangerous threat during an aircraft’s flight. It has been estimated that every aircraft in the U.S. commercial fleet is struck by lightning on average a little over 1 time per 3,000 hours. That translates to a little over once per plane per year. Surges caused by lightning can reach 200,000 amperes (200 kA) of direct current (DC). As long as the aircraft’s ground path remains intact, lightning typically enters the front of the plane or wing tips and exits towards the rear.Similarly, aircraft flying in clouds or precipitation accumulate static electrical charges due to friction. Unless properly mitigated, these charges can potentially generate radio interference thereby disrupting aircraft communications and navigation. Such radio interference negatively impacts electrical circuits due to electromagnetic induction.
Other potential impacts that can compromise the ground path include decreased antenna performance and current path hazards. This post covers more detail about mechanical bonds for Classes A, C, R, L and S (respectively, antennae, current path, electromagnetic interference, lightning, and static electricity).
Aircraft manufacturers publish a detailed aircraft maintenance manual for each model that they build. The manual covers both scheduled and unscheduled maintenance and inspection requirements. Recent advances in milli-ohmmeter technology have resulted in convenient, hand-held portable instrumentation ideal for conducting these inspections. Well designed solutions provide an easy-to-read screen that displays the reading in mΩs while visually reporting the result as PASS or FAIL. Now a bluetooth enabled milli-ohmmeter assures high integrity inspections of critical aircraft assemblies while reducing the time needed to conduct the inspection. This advanced solution captures the necessary readings and seamlessly connects them to any software system from spreadsheets to Quality Management systems.
Aluminum and Composite Structures
As the primary exterior of most aircraft, aluminum conducts electricity. As part of the environmental exposure to oxygen, the metal is also subject to oxidation. Aluminum oxide as opposed to pure metal is an insulator. To maintain the ground path of the aircraft, the structural integrity of rivets and weld seams must be maintained. By contrast, growing numbers of aircraft manufacturers are producing models constructed from composite materials. The composite structure contains a layer of metal mesh that serves as the foundation for the aircraft’s ground path. So the integrity of this mesh must also be maintained.The more that aluminum oxide develops at any one location, the resistance increases as well. If the resistance of a mechanical bond increases beyond the required threshold of 3.0 mΩ, structural integrity is lost. This same standard applies to composite structures. Exceeding this may compromise the plane’s ground path.
To test weld seams and bonds on aluminum structures, use a high-quality milli-ohmmeter. Unlike aluminum structures, composites in aircraft production use an integral mesh in one layer to maintain the ground path. The mesh also introduces resistance. To remain within standard, the composite structure also needs to be tested with a high quality calibrated milli-ohmmeter. The typical test for the integrity of a composite structure is again determined using a high quality milli-ohmmeter. The test is conducted by applying probes between two points specified in the aircraft manufacturer’s maintenance manual and recording the results from the milli-ohmmeter.
The inspection also requires a mega-ohmmeter to measure high resistance value. The objective is to locate any open circuits between two points or high resistance values as specified by the aircraft manufacturer. Static discharger wicks for instance are measured using a mega-ohmmeter. By contrast, the static discharger bases to airframe ground are measured using a milli-ohmmeter.
Lightning: The Most Challenging and Dangerous Impact
All calculations of lightning’s electrical impact are based on a maximum resistance of 3.0 mΩ within the ground path. The energy in a typical lightning strike equals 200 kA (200,000 Amps) x 3.0 mΩ equals 600 V (volts). An intact ground path conducts the lightning from the impact area, usually near the front of the aircraft or the wings to exit towards the rear.The last confirmed commercial plane crash in the U.S. that was directly attributed to lightning occurred in 1967. The lightning caused a catastrophic fuel tank explosion. If the ground path is compromised and fails, potential energy greater than 600V could result in the following dire impacts:
- Sensors may not record properly.
- Data may be corrupted and/or not transmitted accurately.
- Communications may be garbled.
- Instruments may display one or more false positives.
- Controls may be mis-activated.
- And for military aircraft, ordnance may be activated
Preventing Ground Path Issues
Over time, weld and rivet bonds will eventually suffer degradation. Multiple environmental factors can stress these connections including temperature, oxidation, chemical corrosion, vibration and others. The eventual result: Bond sites will register increased electrical resistance above the 3.0 mΩ threshold for non-military aircraft, compromising the ground path. On a side note, the 2.5 mΩ resistance standard has not been empirically determined. It appears to have been developed and adopted as the basis for military aircraft standards.To prevent or mitigate ground path issues, aircraft manufacturers employ multiple methods, the first being lightning diverter strips, also called ground straps or bonding straps. Applied to the aircraft’s radome or other structures, the strips allow a lightning strike to travel safely and directly to the plane’s ground path. The other primary measure installed on all aircraft are static dischargers (also known as “wicks”) that screw into a base mounted on the trailing edges of the control surfaces, wingtips, and the vertical stabilizer.
To test resistance at aircraft bond sites requires a Digital Low Resistance milli-ohmmeter (DLRO). This method measures resistance elements like seam welds and rivets to identify any location with resistance exceeding the 3.0 mΩ standard. Following a lightning strike, the unscheduled maintenance check includes a detailed visual check and replacing any wicks that have been compromised. The inspection team then checks the wick to another one on the craft to measure the resistance and assure the continuity of the ground path using a milli-ohmmeter. If any location records more than the industry standard 3.0 mΩ (2.5 mΩ for military), it compromises the ground path of the aircraft and must be corrected. Left uncorrected, a lightning strike may result in some or all of the extreme consequences noted above.
Static Electricity: Danger of Explosion
Many sources contribute to increased static electricity. These include precipitation, air or dust friction, fluid flow electrification, and charged clouds. Even the human body can carry a charge of up to 0.25 mJ. It takes a surprisingly small amount of energy to ignite fuel vapor, as little as the static electricity from human contact.U = ½ cv² where U = energy stored, c = capacitance, and v = voltage, so…
½ x 0.1µF x 71V² = 0.25mJ = BOOM!
Using an accurate milli-ohmmeter on bond sites and weld seams will identify any site that exceeds the threshold limit of 3.0 mΩ. If none exceed this limit, the risk of a static electricity discharge is greatly reduced. Note that threshold limits vary depending on application. As noted above, the static dischargers serve to both conduct lightning strikes out from the ground path and also discharge any static buildup.
Antenna Bonds
The ground path produces counterpoise for the aircraft’s antenna. If the ground path is below standard, it steals transmitter power and increases the voltage standing wave ratio (VSWR), reducing the antenna’s range. A high-quality, accurate milli-ohmmeter is a shortcut to conduct a quick resistance test to determine that the bond is below 3.0 mΩ. It’s worth noting that the probe design used with the instrument matters; an unwieldy probe design makes it difficult for technicians to access the antenna mounting hardware.Current Path
Return conductors act as power sources. Electrical surges develop when large power loads are activated. This creates a potential fire and arc hazard. Large power loads on an aircraft occur when any of the following systems are activated:- Fuel pumps
- Air conditioning
- Wing de-icer
- Landing Gear
- Engine startup
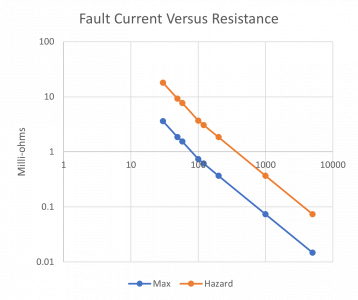
If the maximum current shifts into fault current, one or more arcs can ignite fuel, onboard equipment won’t function, and breakers don’t trip on FAULT. Test the current path with a high-quality, high accuracy milli-ohmmeter.
Measurement Solutions
The Advanced Energy's TEGAM 730A milli-ohmmeter has been designed and produced by the low resistance experts at TEGAM. The company is the largest manufacturer of bond meters for airframe testing in both military and commercial applications. They are also the only bond meters made in the U.S.A.The 730A delivers a high accuracy measurement – ± (0.2% Reading + 0.02% Range). With designed-in Bluetooth, the 730A captures crucial readings and via the seamless data connection, exports results to ANY software system from spreadsheets to Quality Management solutions. This functionality eliminates the integration headache. In addition, a free download is automatically included with advanced new tools supporting iOS, Android, and Windows.
Drawing on our experience, we designed the smallest size bond meter available today. The 730A is portable with a hand-held ergonomic design, for easy one-handed operation. The design integrates our unique low-power techniques to eliminate power cords and battery chargers. The 730A runs on 3 AA batteries for up to 100 hours. The easy-to-read screen includes a battery health indicator to provide ample warning for replacement. The design also includes an auto power-off to extend battery life.
The 730A has a range from 10 milli-ohm to 100 ohms, a resolution of 1 micro-ohm with a PASS/FAIL indication. Each instrument includes a 3-year warranty on Parts and Workmanship plus a 1-year calibration guarantee.
The handheld 730A provides a major testing advantage for producing reliable measurements in tight spaces found in aircraft.
Conclusion
Aircraft flight safety depends on the integrity of the ground path, crucial to prevent failure modes due to hazards. Ground path failures can be caused by lightning, static electricity, EMI, antenna bonds, and current path. Since commercial aircraft are constructed of aluminum, and increasingly of composites, riveting and weld seams are crucial to achieve and maintain structural integrity. This in turn results in a high-integrity ground plane with resistance below the 3.0 mΩ limit.The highly accurate handheld TEGAM 730A milli-ohmmeter provides the solution. It captures these critical readings and eliminates all manual data recording and entry into spreadsheets or Quality Management systems. The ergonomically designed bluetooth enabled instrument fits enables seamless data capture using only one hand. As the only milli-ohmmeter designed and manufactured in the U.S.A., it delivers the excellence, accuracy, and reliability necessary to assure aircraft flight safety.
Advanced Energy Editor
Advanced Energy